Abstrak
Studi ini menyelidiki efek penambahan metakaolin (MK) dan asap silika (SF) pada sifat beton cetak 3D (3DPC) saat masih segar dan mengeras. Lima rancangan campuran disiapkan dengan kadar penggantian MK sebesar 0%, 10%, 12,5%, dan 15%, beserta satu campuran yang mengandung 10% MK dan 5% SF. Metrik kinerja utama meliputi kemampuan alir, kekuatan hijau, kemampuan pompa, retensi bentuk, kemampuan bangun, kemampuan ekstrusi, kekuatan tekan, dan kekuatan ikatan antarlapisan. Hasil penelitian menunjukkan bahwa peningkatan kandungan MK secara umum meningkatkan perolehan kekuatan awal, retensi bentuk, dan kemampuan bangun; namun, dosis MK yang tinggi (15%) berdampak negatif pada kemampuan ekstrusi dan menyebabkan retak yang terlihat. Campuran dengan 10% MK dan 5% SF (MK10SF5) menunjukkan kinerja keseluruhan terbaik, mencapai retensi bentuk yang sangat baik ( S1 = 0,99), kemampuan bangun tertinggi (72 lapisan cetak), dan kekuatan tekan tertinggi: 85,4 MPa untuk spesimen cor dan 78,8, 64,4, dan 73,0 MPa dalam arah X , Y , dan Z , masing-masing, untuk spesimen cetak 3D. Ini juga mencatat kekuatan ikatan interlayer tertinggi sebesar 2,14 MPa. Kinerja superior MK10SF5 dikaitkan dengan efek sinergis MK dan SF, yang meningkatkan pengepakan partikel, kohesi, dan reaktivitas pozzolan. Temuan ini menyoroti potensi MK dan SF dalam mengoptimalkan 3DPC untuk peningkatan kemampuan cetak dan kinerja mekanis.
1. PENDAHULUAN
Beton merupakan material sintetis yang paling banyak digunakan di seluruh dunia dalam industri konstruksi karena hemat biaya, kuat, dan tahan lama. 1 – 3 Bahan baku yang dibutuhkan untuk beton melimpah dan mudah diakses di sebagian besar wilayah, menjadikannya pilihan yang efisien dan praktis untuk berbagai aplikasi konstruksi. Kemudahan akses ini juga memberikan fleksibilitas yang besar bagi arsitek dan desainer, sehingga memungkinkan mereka untuk berinovasi dalam desain. 4 Secara global, konsumsi beton tahunan diperkirakan mencapai sekitar 25 miliar ton, atau lebih dari 3,8 ton per orang per tahun. 5 Namun, produksi dan konsumsi besar-besaran ini menimbulkan tekanan lingkungan yang cukup besar. Produksi semen Portland, komponen penting dalam beton, sangat boros energi dan berkontribusi signifikan terhadap emisi gas rumah kaca, yang diperkirakan mencapai 5%–7% dari emisi CO₂ global. 6 Meskipun menghadapi tantangan lingkungan ini, beton tetap sangat diperlukan sebagai material konstruksi utama, dan kemungkinan akan tetap memegang peranan penting di masa mendatang. 7 Oleh karena itu, peningkatan keberlanjutan struktur beton sangat penting untuk mempertahankan relevansi dan daya saingnya. 8 Lebih jauh lagi, keselamatan pekerja yang terlibat dalam produksi beton di lokasi masih menjadi perhatian, karena tugas-tugas seperti memasang tulangan, mendirikan bekisting, dan pengecoran bentuk-bentuk yang rumit memerlukan tenaga kerja yang terampil, sehingga membuat pekerja terpapar pada bahaya pekerjaan dan potensi cedera. 9 – 12
Manufaktur aditif (AM) menyediakan jalan yang menjanjikan untuk mengatasi beberapa tantangan saat ini dalam industri beton. Selama beberapa dekade terakhir, AM telah melihat kemajuan pesat di berbagai disiplin ilmu dan teknik. 13 – 15 Didefinisikan oleh American Society for Testing and Materials sebagai “proses berbasis lapisan untuk menggabungkan bahan untuk membuat objek dari data model 3D”, 16 Teknologi AM telah menjadi hal yang umum di berbagai sektor, termasuk industri kedirgantaraan, biomedis, dan makanan. 14 , 17 , 18 Beton, mengingat keserbagunaannya sebagai bahan konstruksi, sangat cocok untuk aplikasi manufaktur aditif dalam industri konstruksi. Di antara teknik AM, pencetakan beton 3D (3DCP), juga dikenal sebagai konstruksi beton digital, telah berkembang selama lebih dari 20 tahun, dengan meningkatnya perhatian penelitian dan aplikasi praktis. 19 Metode fabrikasi lapis demi lapis dalam 3DCP, yang menghilangkan kebutuhan akan bekisting, dapat secara signifikan mengurangi waktu konstruksi, biaya, tenaga kerja, penggunaan material, dan pembangkitan limbah. 11 Salah satu faktor penting dalam keberhasilan 3DCP adalah sifat reologi campuran beton, karena sifat-sifat ini harus memenuhi persyaratan kemampuan pemompaan, kemampuan ekstrusi, dan kemampuan pembangunan. 20 Karakteristik tersebut, yang sering kali saling bertentangan, mengharuskan campuran beton cetak 3D memiliki viskositas rendah selama pemompaan dan cepat memperoleh kembali kekuatan setelah ekstrusi, yang menunjukkan perilaku tixotropik. 21
Mayoritas campuran beton cetak 3D yang saat ini tersedia dalam literatur dan industri terdiri dari tiga komponen utama: pengikat, agregat halus, dan air. Dibandingkan dengan beton tradisional, formulasi beton cetak biasanya mengandung kadar pengikat yang lebih tinggi untuk memenuhi persyaratan kemampuan pompa untuk beton cetak 3D (3DPC). 22 Namun, produksi semen Portland biasa (OPC) menghabiskan banyak sumber daya dan energi, menghasilkan sejumlah besar gas rumah kaca, dan menyumbang hampir 10% emisi CO₂ global. 23 Kandungan OPC tinggi yang umum ditemukan dalam formulasi 3DPC dengan demikian mengurangi klaim keberlanjutan dari manufaktur aditif. Seiring kemajuan teknologi AM, ada upaya berkelanjutan untuk berinovasi dengan bahan semen yang sebagian menggantikan semen Portland dengan bahan semen tambahan (SCM) seperti abu terbang, asap silika, dan terak tanur sembur. 24
Dalam beton konvensional, SCM digunakan untuk meningkatkan daya tahan, mengurangi reaksi alkali-silika (ASR), mengurangi panas hidrasi (dan risiko retak termal terkait), dan meningkatkan keberlanjutan dengan menurunkan kandungan karbon dan menggunakan aliran limbah industri sebagai pengganti penimbunan. SCM seperti abu terbang, terak tanur tinggi, asap silika, dan metakaolin telah berhasil dimasukkan ke dalam beton cetak 3D sebagai pengganti semen parsial. 25 – 29 Asap silika (SF), diproduksi sebagai produk sampingan selama pembuatan silikon unsur dan paduan ferosilikon, terutama terdiri dari partikel silikon dioksida (SiO 2 ) amorf, dengan diameter rata-rata berkisar antara 0,1 hingga 0,3 μm. 30 Menambahkan sejumlah kecil SF secara signifikan meningkatkan tegangan luluh dan kemampuan bangun campuran cetak 3D yang mengandung abu terbang. 31 Peningkatan ini disebabkan oleh tingginya luas permukaan SF, yang mendorong reaksi pozzolanik dini dan mempercepat hidrasi semen, sehingga mempercepat perkembangan mikrostruktur terflokulasi. 30 Weng dkk. 32 menemukan bahwa SF efektif dalam mengendalikan reologi campuran 3DPC secara aktif.
Metakaolin (MK), material yang sangat pozzolanik, diperoleh dari kalsinasi lempung kaolinitik pada suhu antara 600 dan 800°C, yang menghasilkan dehidroksilasi kaolinit dan pembentukan MK. 33 Dengan sifat yang sebanding atau melampaui sifat silika fume, MK memiliki ukuran partikel yang umumnya di bawah 5 μm dan sebagian besar terdiri dari SiO 2 dan Al 2 O 3 . 34 Amziane dkk. 35 menunjukkan bahwa peningkatan penggantian klinker dengan MK meningkatkan tegangan luluh statis dan, dengan demikian, meningkatkan kemampuan pembuatan campuran 3DPC. Namun, kebutuhan air MK yang tinggi dapat menghasilkan campuran yang kaku dan kering, yang berdampak buruk pada kemampuan pemompaan dan kemampuan ekstrusi. 35
Uji coba penelitian awal telah menggunakan SCM dalam jumlah besar dalam desain beton yang dapat dicetak 3D. Misalnya, Panda dan Tan 31 mengembangkan campuran menggunakan sistem pengikat terner yang mencakup semen, abu terbang dalam jumlah besar (80% berdasarkan massa), dan sedikit asap silika (2,5% berdasarkan massa) untuk meningkatkan pembentukan struktural. 26 Penelitian ini menunjukkan bahwa “efek bantalan bola” dari abu terbang dapat mengurangi tegangan luluh dan viskositas plastik komposit semen segar, sehingga meningkatkan kemampuan pompa dalam pencetakan 3D. Namun, tingkat penggantian yang berlebihan dapat berdampak buruk pada kemampuan pembentukan dengan menunda pengaturan awal dan hidrasi awal karena berkurangnya flokulasi partikel semen. Sebagai perbandingan, asap silika telah terbukti meningkatkan kemampuan pembentukan dalam sistem pengikat campuran (semen–abu terbang–asap silika) untuk 3DCP. 36 Terak tanur sembur granular yang digiling (GGBS) juga telah digunakan dalam jumlah besar dalam campuran 3DPC. 37 Misalnya, Chaves Figueiredo et al. 38 berhasil menggunakan GGBS, OPC, dan batu kapur untuk mengembangkan komposit semen pengerasan regangan yang dapat dicetak 3D. Demikian pula, Panda dkk. 37 menyelidiki sifat segar dan keras dari campuran yang dapat dicetak dengan bahan baku serupa. Seperti yang dibahas sebelumnya, SCM seperti abu terbang, terak, dan asap silika layak untuk digunakan dalam 3DCP.
Namun, aplikasi MK sebagai pengganti semen untuk pencetakan 3D masih terbatas. MK menunjukkan sifat pengisian yang baik dan aktivitas pozzolan yang signifikan, 39 yang berkontribusi untuk meningkatkan kekuatan hijau dan memperbaiki kinerja mekanis beton. 40 Karakteristik ini menjadikan MK aditif yang menjanjikan untuk menyeimbangkan persyaratan yang bersaing dari ekstrusi dan kemampuan bangun yang khusus untuk pencetakan 3D, sementara juga memastikan sifat mekanis yang kuat setelah pengerasan. Sonebi et al. 41 menunjukkan bahwa MK meningkatkan tegangan luluh, dengan demikian membantu mengendalikan penyebaran aliran pasta semen, dan Janotka et al. 42 meneliti perilaku luluh statis dan dinamis, serta sifat tixotropik campuran pencetakan 3D yang mengandung MK. Akibatnya, penelitian lebih lanjut untuk menggabungkan MK guna mengoptimalkan kemampuan cetak dan sifat mekanis 3DCP diperlukan.
Studi ini bertujuan untuk mengembangkan material semen berkelanjutan untuk 3DCP dengan menggabungkan MK dan SF sebagai pengganti sebagian untuk semen Portland. Efek MK (0%, 10%, 12,5%, dan 15%, bersama dengan campuran yang mengandung 10% MK dan 5% SF) dievaluasi dari berbagai perspektif, dengan fokus pada sifat-sifat baru, seperti kemampuan mengalir, kekuatan hijau, kemampuan memompa, retensi bentuk, kemampuan membangun, dan kemampuan ekstrusi, serta sifat-sifat yang diperkeras, termasuk kekuatan tekan, kekuatan ikatan antarlapisan, dan transformasi kimia suhu tinggi, yang dinilai melalui pengukuran derivatografi. Penelitian ini memberikan wawasan tentang perilaku reologi dan mekanis campuran beton cetak 3D yang mengandung MK dan SF, yang berkontribusi pada kemajuan praktik berkelanjutan dalam manufaktur aditif untuk konstruksi.
2 PROGRAM EKSPERIMENTAL
2.1 Bahan dan prosedur pencampuran
Bahan semen primer yang digunakan dalam studi ini adalah semen Portland CEM I 52,5 N, MK, dan SF. Semen Portland diproduksi oleh Duna-Dráva Company (Duna-Dráva Cement, Hungaria, Heidelberg Cement Group) yang mematuhi persyaratan standar MSZ EN 196-2. 43 MK diproduksi dengan kalsinasi kaolin alami pada kisaran suhu tipikal 600–800°C. Jenis MK yang digunakan adalah Metaver N, diproduksi oleh Newchem Ltd. (Austria), dan disediakan oleh Meselia Ltd. (Hungaria), memiliki warna putih yang menarik (Gambar 1b ), dan mengikuti persyaratan standar MSZ 4798. 44 SF adalah bahan produk sampingan yang dihasilkan dari produksi logam ferosilikon dan paduan silikon; sekitar 30% massa silikon yang diproduksi. Warna SF yang digunakan adalah abu-abu gelap kebiruan (Gambar 1c ), dengan partikel bulat yang sangat halus. SF yang diaplikasikan dalam penelitian ini (Sikafume-HR) dipasok dari perusahaan Sika. Tabel 1 memberikan komposisi kimia PC, MK, dan SF yang disediakan oleh produsen. Gambar 2 memberikan pola difraksi sinar-X (XRD) dari bahan baku. XRD dilakukan pada difraktometer sinar-X serbuk PANanalytical Xpert Pro MPD dengan detektor X’celerator, dengan radiasi Cu-Kα yang dioperasikan pada 40 kV dan 30 mA, untuk nilai 2 θ antara 3° dan 85°. Pola XRD memberikan komposisi fase khas untuk semen, metakaolin, dan silika fume. CEM I 52,5 N terdiri dari mineral klinker (C3S , β- C2S , C3A dan C4AF ) , dan sebagai tambahan dari komponen utama ini, gipsum dan kalsit hadir sebagai komponen minor. Metakaolin terdiri dari mullite dan α-kuarsa, dan fase amorf. Pola XRD dari asap silika menunjukkan bahwa material tersebut sebagian besar amorf. Analisis distribusi ukuran partikel (PSD) dilakukan dengan Penganalisis Distribusi Ukuran Partikel Laser Scattering HORIBA LA-950. PSD bahan baku diberikan pada Gambar 3 .
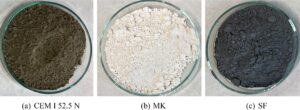
Oksida (wt%) | CEM saya 52,5 N | Bahasa Inggris | Bahasa Inggris |
---|---|---|---|
SiO2 (SiO3 ) | pukul 20.59 | 52–53 | 96.43 |
Al2O3 | 5.55 | 43–44 | 0.7 |
Fe2O3 | 3.21 | 1.5 | 0,073 tahun |
CaO | 65.02 | 0.5 | 0,78 |
MgO | 1.44 | 0.4 | 0,70 |
JADI 3 | 2.88 | – | 0,038 |
K2O | 0,78 | 2 | 1.28 |
Cl | 0,0048 pukul 0,0048 | – | – |
Na2O | – | 0.1 | – |
TiO2 adalah | – | 1 | – |
Surat Keterangan | 1.59 | 2.8 | |
Kepadatan (g/ cm3 ) | 3.17 | 2.6 | 2.15 |
Luas Permukaan (cm2 / g) | 4500 | 22.000 | 20.000 |
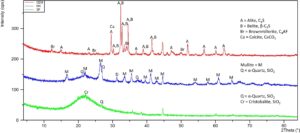
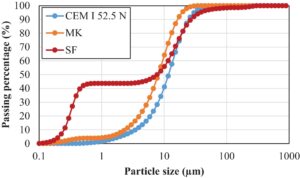
Karena keterbatasan ukuran sistem nosel selang pompa, pasir kuarsa dengan diameter maksimum 1,2 mm dan modulus kehalusan 2,99 digunakan sebagai agregat dalam penelitian ini. Superplasticizer berbasis eter polikarboksilat (MasterGlenium 300, BASF) dipilih dalam penelitian ini.
Berdasarkan bahan baku yang disebutkan, lima proporsi campuran ditunjukkan pada Tabel 2. Penelitian ini menggunakan empat penggantian MK yang berbeda (0%, 10%, 12,5%, dan 15%) yang diwakili oleh MK0, MK10, MK12,5, MK15; dan berdasarkan hasil uji coba, satu dengan 10% MK dan 5% SF, diwakili oleh MK10SF5. Rasio pasir/pengikat (s/b) sebesar 1,5, rasio air/pengikat (w/b) sebesar 0,33, dan 0,45% dari massa pengikat SP dijaga sama untuk semua campuran. Campuran segar disiapkan menggunakan planetary mixer (HOBART) dengan mengikuti prosedur yang diberikan pada Tabel 3. Waktu pencampuran suspensi (air dan SP) dengan komponen kering ditetapkan sebagai waktu nol ( t = 0 menit).
Jenis | Bahan pengikat | Pasir | Air | Bahasa Inggris | ||
---|---|---|---|---|---|---|
CEM I 52,5 N (berat%) | MK (berat %) | Berat jenis SF (berat %) | (berat %) | (berat %) | (berat %) | |
MK0 | 100 | angka 0 | angka 0 | 150 | 33 | 0.45 |
MK10 | 90 | 10 | angka 0 | 150 | 33 | 0.45 |
MK12.5 | 87.5 | 12.5 | angka 0 | 150 | 33 | 0.45 |
MK15 | 85 | 15 | angka 0 | 150 | 33 | 0.45 |
MK10SF5 | 85 | 10 | 5 | 150 | 33 | 0.45 |
Waktu (menit) | Prosedur pencampuran |
---|---|
-2 | Campur bahan kering dengan kecepatan rendah menggunakan mixer planet |
angka 0 | Tambahkan fase cair (air dan SP) |
3 | Berhenti sebentar, kikis bagian bawah mangkuk. Aduk dengan kecepatan rendah |
7 | Berhenti sebentar, kikis bagian bawah mangkuk. Aduk dengan kecepatan tinggi |
10 | Berhenti, mulai uji/cetak/cetak |
2.2 Pengaturan pencetakan
Pencetakan dilakukan dengan menggunakan robot lengan enam sumbu dari ABB (Gambar 4 ). Robot dapat melakukan operasi pencetakan dengan kemampuan rotasi 360°, meliputi diameter horizontal 3 m dan tinggi vertikal 3 m, dan dengan ekstensi, dapat mencapai hingga 6 m. Kecepatan pencetakan lengan robot dapat diatur antara 0 dan 200 mm/s. Lengan robot terhubung ke pengontrol yang mengatur gerakan kepala lengan robot.
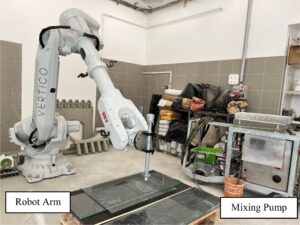
Pompa pencampur dari MAI (Gambar 4 ) digunakan dalam makalah ini. Pompa pencampur ini terdiri dari beberapa modul: keranjang untuk bahan baku kering, pengumpan sekrup untuk bahan baku kering, dan tangki air dengan dispenser yang memungkinkan penambahan air ke dalam campuran, dan campuran tersebut masuk ke sistem pemompaan. Sistem pemompaan bertanggung jawab untuk mengangkut campuran ke kepala cetak dan terdiri dari motor, hopper dengan sekrup pengumpan, pompa, dan sambungan selang. Dalam penelitian ini, campuran segar disiapkan dengan menggunakan mixer Hobart luar dan dimuat secara manual ke dalam sistem pemompaan untuk memastikan rasio w/d yang tepat ditambahkan, selain menjaga prosedur pencampuran yang sama. Selang fleksibel dengan diameter dalam 25 mm dan panjang 5 m digunakan untuk menghubungkan pompa dengan nosel yang dipasang pada kepala cetak robotik di bagian ujung sumbu z . Nosel melingkar dengan diameter 25 mm digunakan dalam penelitian ini. Laju aliran, kecepatan cetak, dan tinggi lapisan dipertahankan sama untuk semua campuran masing-masing sebesar 1,5 L/menit, 84 mm/detik, dan 10 mm.
2.3 Prosedur pengujian
2.3.1 Uji aliran
Pengujian dilakukan sesuai dengan EN 1015-3. 45 Cetakan mini-kerucut dengan diameter internal atas 70 mm, diameter internal bawah 100 mm, dan tinggi 60 mm digunakan dalam pengujian ini. Sebelum pengujian, permukaan bagian dalam cetakan dilumasi dengan oli cetakan. Setengah dari cetakan diisi dengan campuran segar, dan kemudian campuran segar diaduk menggunakan tongkat kayu sekitar 10 kali. Prosedur yang sama diulang untuk bagian kedua cetakan. Bahan berlebih perlahan-lahan dikikis dengan sekop. Setelah cetakan dilepas, meja dijatuhkan 15 kali dalam waktu 15 detik. Diameter sebaran dicatat melalui pengukuran dua arah tegak lurus. Untuk setiap campuran, pengujian ini dilakukan untuk setiap umur bahan dari 10 hingga 60 menit, dengan interval 10 menit. bahan segar disegel dalam kantong plastik untuk mencegah penguapan air. Tiga pengulangan dilakukan untuk setiap umur.
2.3.2 Uji kekuatan hijau
Uji kekuatan hijau dilakukan untuk menilai perkembangan kekuatan selama jam pertama untuk campuran. Campuran segar disiapkan dan kemudian dituangkan ke dalam cetakan silinder dengan diameter internal 60 mm dan tinggi 60 mm. Semprotan silikon awalnya digunakan untuk melapisi cetakan sebelum mengisi mortar segar. Semua sampel dipadatkan secara manual untuk mengurangi jumlah gelembung udara. Sampel kemudian disimpan dalam kantong plastik tertutup dan dikeluarkan dari cetakan tepat sebelum pengujian kekuatan hijau. Mesin uji universal Instron yang dilengkapi dengan sel beban 10 kN digunakan untuk melakukan uji kekuatan hijau. Pengujian dilakukan dengan kompresi konstan pada kecepatan 15 mm/menit hingga kompresi 25 mm atau pengurangan gaya tekan hingga 95%. Untuk setiap campuran, pengujian ini dilakukan untuk setiap umur material dari 10 hingga 60 menit, dengan interval 10 menit. Tiga pengulangan dilakukan untuk setiap umur.
2.3.3 Kemampuan pompa dan retensi bentuk
Kemampuan pompa mengacu pada kemampuan campuran untuk diangkut melalui pipa di bawah tekanan. Untuk mengevaluasi dampak bahan semen pada kemampuan pompa beton selama pencetakan 3D, tekanan dicatat untuk setiap campuran selama proses pencetakan. Sementara itu, retensi bentuk mengacu pada kemampuan lapisan beton yang diekstrusi untuk mempertahankan bentuk penampang melintangnya, yang sesuai dengan penampang melintang nosel. Untuk menilai retensi bentuk, struktur persegi panjang berongga dengan dimensi lebar 200 mm dan panjang 400 mm dicetak (Gambar 5 ). Ini diverifikasi dengan mengukur lebar segmen yang dicetak menggunakan jangka sorong. Rasio retensi bentuk ( S 1 ), diperkenalkan oleh Panda et al., 46 didefinisikan sebagai:
di mana W f adalah lebar rata-rata filamen yang diekstrusi (diukur pada empat sisi), dan W n adalah lebar nosel. Semakin dekat nilai S 1 ke 1, semakin baik retensi bentuknya.
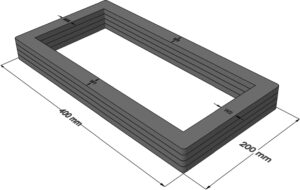
2.3.4 Kemampuan membangun dan ekstrudabilitas
Kemampuan bangun mengacu pada kemampuan struktur cetak untuk dibangun lapis demi lapis tanpa kegagalan. Saat ini, tidak ada standar yang ditetapkan untuk menilai kemampuan bangun vertikal beton. Untuk memeriksa efek berbagai campuran beton segar pada kemampuan bangun, jumlah lapisan filamen cetak digunakan sebagai indikator, dengan kemampuan bangun dianggap terganggu ketika deformasi atau keruntuhan yang terlihat terjadi pada struktur. Seperti yang ditunjukkan pada Gambar 6 , kemampuan bangun dievaluasi dengan mencetak silinder berongga dengan diameter eksternal 150 mm. Di sisi lain, kemampuan ekstrusi adalah kemampuan beton untuk melewati nosel penyempitan di bawah tekanan tanpa segregasi, menghasilkan filamen kontinu. Campuran dianggap berhasil dalam tahap ekstrusi jika filamen dapat diekstrusi terus menerus, tanpa penyumbatan nosel atau kerusakan filamen.
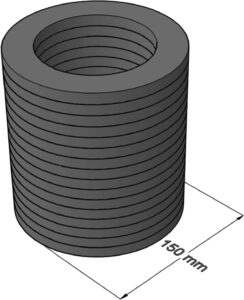
2.3.5 Uji kuat tekan
Dinding berukuran 750 × 100 × 50 mm 3 dicetak menggunakan sistem yang dijelaskan dalam Bagian 2.2 (Gambar 7 ). Dari dinding cetak ini, kubus berukuran 40 × 40 × 40 mm 3 digergaji. Untuk memperhitungkan sifat mekanis anisotropik dari mortar cetak, sampel diuji dalam arah X , Y , dan Z (Gambar 7 ), dengan empat pengujian berulang yang dilakukan di setiap arah. Nilai rata-rata dihitung dari pengujian ini. Secara total, 12 kubus cetak disiapkan dan diuji untuk setiap campuran. Selain itu, empat kubus cor dengan ukuran yang sama disiapkan dan diuji untuk perbandingan. Semua sampel diawetkan pada suhu kamar. Kekuatan tekan pada 28 hari diukur sesuai dengan EN 12390-3 47 pada laju pembebanan 2,4 kN/s.
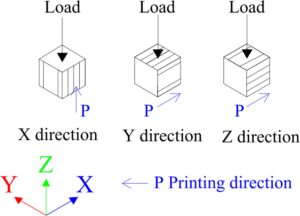
2.3.6 Uji kekuatan ikatan antar lapisan
Uji tarik uniaxial dilakukan untuk menentukan kekuatan ikatan sampel yang dicetak. Satu hari setelah pencetakan, empat prisma persegi panjang dengan dimensi 60 mm ( P ) × 25 mm ( L ) × 40 mm ( T ) (Gambar 8a ) diekstraksi dari struktur cetakan yang dijelaskan dalam Bagian 2.3.3 menggunakan mesin pemotong. Sampel-sampel ini kemudian diawetkan pada suhu ruangan selama 28 hari. Kekuatan ikatan interlayer dievaluasi dengan menguji kekuatan tarik uniaxial dari spesimen lapisan ganda, seperti yang ditunjukkan pada Gambar 8b . Takik 5 mm dibuat di kedua sisi spesimen untuk mengamankan klem dan memastikan bahwa kegagalan terjadi pada interlayer. Klem dipasang ke mesin uji universal, yang menarik spesimen dengan kecepatan 0,5 mm/menit hingga gagal.
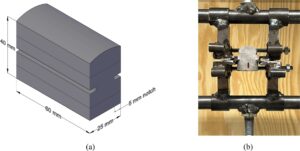
2.3.7 Uji termogravimetri
Analisis termogravimetri yang diterapkan adalah metode analisis termal di mana perubahan sifat fisik dan kimia bahan diukur sebagai fungsi dari peningkatan suhu (dengan laju pemanasan konstan). Selain itu, perubahan fase diikuti dengan metode termogravimetri (TG), termogravimetri derivatif (DTG), dan termoanalisis diferensial (DTA), menggunakan instrumen MOM Derivatograph-Q 1500 TG/DTG/DTA. Selama pengukuran, krusibel korundum digunakan dan Al2O3 sebagai bahan referensi dengan massa sekitar 300 mg. Laju pemanasan sampel adalah 10 °C hingga 1000°C di atmosfer udara. Sampel termogravimetri digiling menjadi bubuk halus dan diukur segera setelah penggilingan dengan TG/DTA untuk memastikan kesehatan sampel dari karbonasi. Bubuk yang diuji diambil dari kubus yang dicetak dan dihancurkan setelah uji kompresi dan dipilih dari inti spesimen. Pengujian dilakukan pada sampel pada usia 28 hari.
3 HASIL DAN PEMBAHASAN
3.1 Kemampuan mengalir
Gambar 9 mengilustrasikan hasil uji alir untuk campuran pada interval yang berbeda dalam jam pertama. Campuran MK0, yang hanya mengandung CEM I 52,5 N tanpa substitusi MK atau SF, awalnya menunjukkan nilai alir tertinggi. Seiring berjalannya waktu, diameter penyebaran campuran ini secara bertahap menurun, yang menunjukkan penurunan kemampuan kerja seiring bertambahnya waktu istirahat. Kehilangan kemampuan kerja ini disebabkan oleh pengerasan campuran secara bertahap, yang terjadi karena terbentuknya jembatan kalsium silikat hidrat (C–S–H) di antara partikel. Jembatan C–S–H ini menciptakan jaringan yang kaku dan saling terhubung di dalam material. Meskipun jaringan ini tetap rapuh di bawah gaya geser yang relatif tinggi, metode table-dropping mungkin tidak menghasilkan energi geser yang cukup untuk memutus semua koneksi antar-partikel ini. 48 , 49
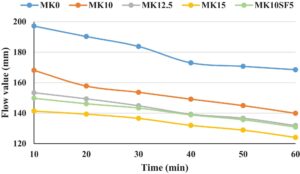
Untuk campuran MK10, MK12.5, dan MK15, di mana proporsi semen yang lebih besar diganti dengan MK, penurunan yang nyata dalam kemampuan alir diamati bersamaan dengan peningkatan stabilitas bentuk dari waktu ke waktu. Penurunan nilai alir berbanding lurus dengan peningkatan kandungan Metakaolin. Hal ini disebabkan oleh reaksi pozolanik MK, yang mempercepat proses pengerasan dan mengakibatkan hilangnya kemampuan kerja lebih cepat.
Campuran MK10SF5, yang mengandung 10% MK dan 5% SF, menunjukkan retensi aliran yang lebih baik dibandingkan dengan MK15. Peningkatan retensi aliran ini dapat dikaitkan dengan ukuran partikel yang lebih halus dan luas permukaan silika fume yang lebih tinggi, yang meningkatkan stabilitas campuran dengan meningkatkan kohesi antar partikel.
3.2 Hasil kekuatan hijau
Perkembangan kekuatan hijau dalam jam pertama dapat digunakan sebagai indikator kemampuan membangun struktur campuran yang tepat. Gambar 10a–e menunjukkan kurva beban–perpindahan rata-rata campuran baru MK0, MK10, MK12.5, MK15, dan MK10SF5 dari usia 10 hingga 60 menit. Puncak awal dalam kurva beban–perpindahan menunjukkan titik saat material mulai menahan beban yang diberikan secara efektif. Pada tahap ini, campuran beton baru mengembangkan kohesi dan ikatan antar partikel yang cukup, sehingga menghasilkan peningkatan kapasitas menahan beban. Setelah mencapai beban puncak, kurva menunjukkan penurunan kapasitas menahan beban, yang dapat dikaitkan dengan struktur internal beton baru yang mulai luluh atau rusak. Perilaku ini sering dikaitkan dengan retakan mikro, terlepasnya ikatan, atau tergelincirnya partikel dalam campuran. Mortar baru mungkin mengalami sedikit kegagalan internal, seperti retakan atau fraktur, yang mengurangi kemampuannya menahan beban, yang menyebabkan penurunan kurva. Kurva kemudian mulai meningkat lagi setelah penurunan awal. Peningkatan ini dapat dijelaskan dengan pemadatan ulang atau pemadatan material. Saat perpindahan berlanjut, partikel-partikel dalam campuran mungkin menata ulang atau memadat lebih jauh, menutup retakan mikro atau rongga yang awalnya terbentuk. Penataan ulang ini mengarah pada pemulihan kapasitas menahan beban material, yang tercermin dalam peningkatan kurva.
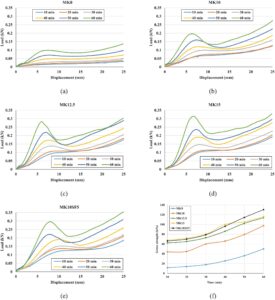
Gambar 10f menunjukkan kekuatan hijau setiap campuran pada usia yang berbeda. Kekuatan hijau dapat didefinisikan sebagai beban puncak dibagi dengan luas permukaan silinder. Campuran MK0 (tanpa substitusi MK atau SF) dimulai dengan kekuatan hijau terendah pada 10 menit (11 kPa) dan secara bertahap meningkat menjadi 50 kPa pada 60 menit. Laju peningkatan kekuatan yang relatif lambat merupakan ciri khas campuran yang hanya mengandalkan CEM I 52,5 N, karena tidak ada bahan pozolan tambahan untuk mempercepat proses hidrasi usia dini. Peningkatan kekuatan secara bertahap sejalan dengan pengerasan beton yang diharapkan saat hidrasi berlangsung, tetapi tidak memiliki perkembangan kekuatan awal yang cepat, yang penting untuk mencapai retensi bentuk dan kemampuan bangun yang tinggi. Namun, mengganti sebagian semen dengan MK meningkatkan kekuatan usia dini karena reaksi pozolannya, yang berkontribusi pada pembentukan gel kalsium silikat hidrat (C–S–H) tambahan, yang meningkatkan ikatan partikel. Campuran MK10 (substitusi metakaolin 10%) menunjukkan peningkatan substansial dalam kekuatan hijau dibandingkan dengan MK0, dimulai pada 44 kPa pada 10 menit dan meningkat menjadi 98 kPa pada menit ke-60.
Kekuatan awal MK10 yang lebih tinggi menunjukkan bagaimana bahkan substitusi kecil semen dengan MK secara signifikan mempercepat proses pengerasan dan meningkatkan sifat mekanis campuran segar. Kekuatan hijau dari campuran MK15 dan MK10SF5 cukup dekat dan jauh lebih tinggi daripada campuran lainnya. Campuran MK15 menunjukkan nilai yang sedikit lebih tinggi dibandingkan dengan campuran MK10SF5 hingga usia material 40 menit. Namun, setelah tanda 40 menit, kekuatan hijau MK10SF5 melampaui MK15. Ini dapat dijelaskan dengan adanya asap silika di MK10SF5. Asap silika, dengan partikelnya yang sangat halus, meningkatkan pengepakan partikel dan meningkatkan reaktivitas keseluruhan campuran pada tahap selanjutnya. Ini meningkatkan kohesi dan kekuatan, yang memungkinkan MK10SF5 untuk mengembangkan kekuatan hijau yang lebih tinggi saat campuran terus menua. Asap silika juga berkontribusi pada peningkatan pembentukan ikatan antara partikel, yang menjadi lebih jelas seiring berjalannya waktu.
3.3 Hasil pemompaan dan retensi bentuk
Hasil pemompaan menunjukkan bahwa campuran dengan dosis MK yang lebih tinggi memerlukan tekanan ekstrusi yang jauh lebih tinggi untuk mencapai laju aliran yang sama dibandingkan dengan campuran dengan kandungan MK yang lebih rendah. Penambahan MK dan SF ke dalam campuran beton meningkatkan tekanan yang diperlukan untuk pemompaan selama pencetakan 3D, dengan dosis yang lebih tinggi menghasilkan hambatan aliran yang lebih besar. Sementara campuran semen murni tidak memerlukan tekanan untuk memompa, pengenalan 10%–15% MK meningkatkan kebutuhan tekanan secara substansial, mencapai hingga 10 bar dengan MK15. Khususnya, menggabungkan 10% MK dengan 5% SF memerlukan tekanan yang lebih rendah daripada MK15 saja, yang menunjukkan bahwa campuran bahan semen yang seimbang dapat meningkatkan pemompaan dan kinerja material.
Gambar 11a mengilustrasikan retensi bentuk dari campuran yang berbeda. Rasio retensi bentuk ( S 1 ) adalah parameter penting untuk mengevaluasi stabilitas dimensi lapisan 3DPC yang diekstrusi. Rasio ini membandingkan lebar segmen yang dicetak dengan lebar nosel, dengan nilai yang mendekati 1 menunjukkan retensi bentuk yang lebih baik. Campuran MK0 (semen murni) dikeluarkan dari analisis karena ketidakmampuannya untuk mempertahankan bentuk, seperti yang ditunjukkan pada Gambar 11b . Meskipun dapat dicetak, campuran ini terlalu cair, menyebabkan lapisan menyebar dan kehilangan geometri yang diinginkan.

Penambahan 10% MK meningkatkan retensi bentuk, meskipun campuran MK10 menunjukkan nilai S 1 tertinggi , yang menunjukkan sedikit pengembangan berlebih dari filamen yang diekstrusi di luar penampang nosel. Campuran MK12,5 memiliki nilai S 1 yang sedikit lebih rendah daripada MK10, yang menunjukkan pengurangan pengembangan. Peningkatan kandungan MK (12,5%) menghasilkan campuran yang lebih kaku dan lebih terkendali, yang meningkatkan retensi bentuknya. Meskipun beberapa pengembangan masih terjadi, pengembangannya lebih terkendali daripada campuran MK10. Hal ini menunjukkan bahwa peningkatan kandungan MK membantu meningkatkan retensi bentuk, meskipun akurasi dimensi penuh tetap menjadi tantangan.
Campuran MK15 menunjukkan retensi bentuk terendah, dengan nilai S 1 di bawah 1, yang menunjukkan bahwa campuran menyusut, gagal mempertahankan luas penampangnya. Kandungan MK yang tinggi (15%) kemungkinan menyebabkan pengerasan cepat, yang menyebabkan penyusutan dini karena tekanan internal. Meskipun komposisi ini dapat menguntungkan perolehan kekuatan dini, namun hal ini mengorbankan stabilitas dimensi, yang sangat penting untuk presisi dalam aplikasi pencetakan 3D.
Campuran MK10SF5, yang mengandung 10% MK dan 5% SF, menunjukkan retensi bentuk yang hampir sempurna, dengan nilai S 1 mendekati 1. Penambahan SF, dengan ukuran partikelnya yang halus dan luas permukaan yang tinggi, meningkatkan kohesi campuran, mencegah pemuaian berlebih. Kombinasi MK dan SF yang seimbang ini mengoptimalkan kemampuan kerja dan stabilitas dimensi, menjadikan MK10SF5 campuran yang paling cocok untuk pencetakan 3D di antara yang diuji.
3.4 Hasil buildability dan ekstrudabilitas
Gambar 12 menunjukkan hasil kemampuan bangun campuran. Campuran MK0 tanpa substitusi MK menunjukkan kemampuan bangun yang buruk, mencapai kurang dari 2 lapisan sebelum kegagalan. Ini menunjukkan bahwa campuran semen saja kemungkinan memiliki viskositas dan kohesi yang tidak memadai untuk membangun lapisan. Tanpa bahan tambahan seperti MK atau SF, campuran tersebut mungkin tidak memiliki sifat tixotropik yang diperlukan untuk mendukung lapisan tambahan, yang menyebabkan keruntuhan dini. Dengan mengganti 10% semen dengan metakaolin, kemampuan bangun meningkat secara signifikan mencapai 23 lapisan. Metakaolin meningkatkan viskositas dan kohesivitas campuran karena sifat pozzolannya, yang berkontribusi pada kepadatan pengepakan yang lebih baik dan pengembangan kekuatan awal. Ini memungkinkan lapisan untuk saling menempel lebih efektif, mendukung lebih banyak lapisan sebelum kegagalan. Peningkatan lebih lanjut kandungan metakaolin menjadi 12,5% menghasilkan peningkatan yang lebih besar, dengan 42 lapisan tercapai. Peningkatan kandungan MK lebih lanjut meningkatkan tixotropi dan pembangunan struktural campuran. Aktivitas pozzolan yang lebih tinggi berkontribusi pada ikatan antar lapisan yang lebih baik dan kekuatan awal, yang memungkinkan campuran untuk mendukung lebih banyak lapisan.
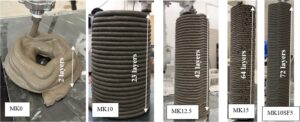
Dengan 15% MK, campuran mencapai 64 lapisan, yang menunjukkan kemampuan bangun yang sangat baik dalam hal jumlah lapisan. Namun, ekstrudabilitas yang buruk diamati dengan banyak retakan, Gambar 13. Ini menunjukkan bahwa sementara kandungan MK yang tinggi meningkatkan penumpukan struktural, itu juga membuat campuran terlalu kaku atau getas, yang menyebabkan kesulitan dalam ekstrusi dan peningkatan kerentanan terhadap retak. Campuran mungkin menjadi terlalu kental atau kehilangan beberapa plastisitas, yang mengakibatkan adhesi lapisan yang buruk dan pembentukan retakan selama atau setelah pencetakan. Campuran dengan 10% metakaolin dan 5% silika fume mencapai kemampuan bangun tertinggi dengan 72 lapisan, dan juga memiliki ekstrudabilitas terbaik. Kombinasi MK dan SF kemungkinan menyeimbangkan sifat campuran dengan sempurna. Metakaolin berkontribusi pada kekuatan awal dan penumpukan struktural, sementara silika fume, yang dikenal karena ukuran partikelnya yang sangat halus dan reaktivitas pozzolan yang tinggi, lebih jauh meningkatkan kekompakan dan kepadatan pengepakan campuran. Asap silika juga meningkatkan kemampuan alir dan kerja campuran, mencegah kerapuhan dan keretakan yang berlebihan, sehingga menghasilkan lapisan yang lebih banyak dan kualitas cetak keseluruhan yang lebih baik.
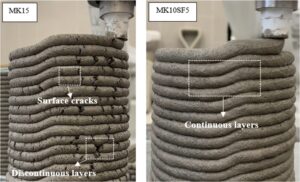
3.5 Hasil kekuatan tekan
Gambar 14 mengilustrasikan hasil kekuatan tekan 28 hari untuk kubus cor dan 3DPC yang terbuat dari campuran yang berbeda. Penambahan MK memiliki dampak yang nyata pada kekuatan tekan di semua sampel. Pada kubus cor, kekuatan tekan meningkat sekitar 4%, 15%, dan 6% untuk campuran MK10, MK12.5, dan MK15, berturut-turut. Peningkatan ini disebabkan oleh sifat pozzolan Metakaolin yang sangat reaktif, yang meningkatkan kekuatan dengan mendorong pembentukan gel C–S–H tambahan yang mengisi pori-pori mikro dalam matriks beton. Peningkatan kekuatan yang signifikan dari MK10 ke MK12.5 menunjukkan bahwa penambahan Metakaolin hingga 12,5% secara optimal meningkatkan reaktivitas pozzolan dan pemadatan matriks. Namun, pada 15% MK, sedikit penurunan kekuatan dapat dikaitkan dengan retakan mikro atau tegangan internal dari kandungan Metakaolin yang berlebihan, yang dapat mengganggu hidrasi dan ikatan matriks dari waktu ke waktu. Khususnya, campuran MK10SF5 mencapai kekuatan cor tertinggi, menunjukkan peningkatan sekitar 19%.
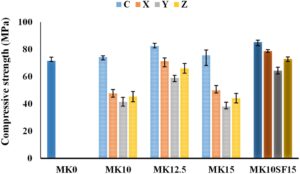
Seperti yang ditunjukkan pada Gambar 14 , kuat tekan kubus cor secara konsisten lebih tinggi daripada kubus cetak 3D. Perbedaan ini sejalan dengan temuan dari penelitian sebelumnya, 25 , 50 – 53 yang mengaitkan kekuatan yang lebih rendah dalam sampel cetak 3D dengan ikatan antarlapisan yang lebih lemah dan presisi pencetakan yang berkurang. 50 Selain itu, anisotropi dalam kuat tekan diamati dalam sampel cetak, dengan kekuatan bervariasi tergantung pada arah pemuatan. Secara khusus, arah X (sejajar dengan lintasan pencetakan) menunjukkan kuat tekan yang lebih tinggi dibandingkan dengan arah Y dan Z , kemungkinan karena penyelarasan partikel yang lebih baik dan pemadatan sepanjang sumbu pencetakan. Nerella et al. 54 juga mencatat bahwa pemadatan yang disebabkan oleh berat lapisan yang berurutan berperan dalam meningkatkan kuat tekan sepanjang sumbu ini.
Peningkatan kekuatan tekan pada sampel cetakan MK10 dan MK12.5 menunjukkan bahwa metakaolin meningkatkan ikatan antarlapisan dan integritas struktural elemen cetakan 3D. Namun, campuran MK15, dengan 15% MK, menunjukkan kekuatan yang berkurang di semua arah, kemungkinan karena kekakuan yang berlebihan dan tekanan internal yang mendorong penyusutan dan retakan mikro di dalam lapisan cetakan. Sebaliknya, campuran MK10SF5, yang menggabungkan 10% MK dengan 5% silika fume, tampaknya menyeimbangkan kekuatan dan stabilitas dimensi dalam sampel cetakan, yang mengarah ke kekuatan tekan yang lebih seragam dan lebih tinggi di semua arah karena pengepakan partikel yang ditingkatkan dan kohesi campuran.
3.6 Hasil kekuatan ikatan antar lapisan
Kekuatan ikatan tarik yang lebih tinggi menunjukkan daya rekat yang lebih baik di antara lapisan, yang sangat penting untuk integritas struktural objek yang dicetak. Kekuatan ikatan yang tinggi biasanya menunjukkan bahwa campuran tersebut memiliki kohesi dan ikatan antarlapisan yang baik, yang dapat ditingkatkan dengan proporsi campuran yang optimal, kondisi pengawetan, dan sifat material baru. Sementara kekuatan ikatan yang lebih rendah menunjukkan daya rekat yang lebih lemah di antara lapisan, yang dapat mengakibatkan titik lemah atau delaminasi potensial dalam struktur. Hal ini dapat disebabkan oleh masalah seperti konsistensi material yang buruk, pencetakan yang tertunda di antara lapisan (waktu jeda di antara lapisan), atau desain campuran yang tidak memadai.
Gaya puncak dari setiap uji tegangan uniaxial dikumpulkan dan dibagi dengan luas penampang (15 × 60 mm 2 ) untuk menghitung kekuatan ikatan tarik uniaxial. Hasil perhitungan disajikan dalam Gambar 15 . Peningkatan kandungan MK umumnya memperbaiki kekuatan awal dan meningkatkan kekuatan ikatan karena reaksi pozzolan yang memperbaiki pengepakan dan kohesi partikel. Namun, MK yang berlebihan (seperti pada MK15) mengurangi kemampuan kerja; ekstrudabilitas dan retensi bentuk yang lebih buruk menunjukkan kekuatan ikatan yang lebih rendah. Metakaolin yang berlebihan dapat menyebabkan kerapuhan atau mengurangi plastisitas, sehingga menghambat ikatan yang tepat antara lapisan. Sementara itu, MK10SF5 menunjukkan kekuatan ikatan tertinggi karena efek sinergis metakaolin dan silika fume, yang memperbaiki kohesi di dalam lapisan dan adhesi di antara keduanya.
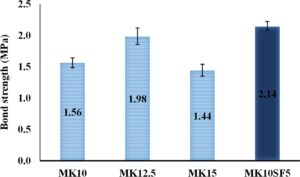
3.7 Hasil termogravimetri
Uji termogravimetrik diteliti pada umur 28 hari. Gambar 16a–f menunjukkan hasil pengujian. Pada Gambar 16a kurva DTG ditunjukkan dalam kasus sampel yang mengandung metakaolin (MK10, MK12.5, MK15, dan MK10SF5). Gambar 16b–f menunjukkan kurva TG, DTG, dan DTA untuk setiap campuran secara terpisah.
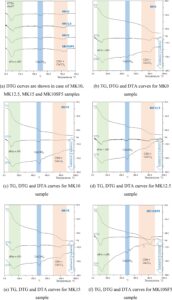
Analisis termoanalitik mengungkap tiga tahap penurunan berat. Tahap pertama, antara sekitar 50 dan 250°C, berhubungan dengan dehidrasi fase Aft (ettringite) dan AFm (monosulfate) serta gel C–S–H, yang mengakibatkan penurunan berat (72). Tahap kedua, antara sekitar 450 dan 550°C, disebabkan oleh dehidrasi kalsium hidroksida (Portlandite, CH), yang menyebabkan penurunan berat lebih lanjut. Tahap ketiga, yang terjadi pada suhu antara sekitar 650 dan 900°C, dikaitkan dengan dekomposisi termal lebih lanjut dari CSH dan CaCO₃. 55
Data termoanalitik yang dihitung dari kurva TG dirangkum dalam Gambar 17. Air yang terikat secara kimia ( W b ) dan derajat hidrasi ( α ) dihitung menggunakan metodologi Bhatty 56 seperti yang dijelaskan dalam Persamaan (1) dan (2):
di mana L dh menunjukkan kehilangan massa karena dehidrasi AFt, AFm, dan CSH (50–250 °C), L dx sesuai dengan dehidrasi Portlandite (450–550 °C), dan L dc memperhitungkan kehilangan massa dari dekomposisi termal (650–900 °C). Selain kehilangan massa termoanalitik selama uji termal, air yang terikat secara kimia dan derajat hidrasi juga diberikan dalam Tabel 4. Kita dapat menyatakan bahwa derajat hidrasi yang lebih rendah dikaitkan dengan sampel referensi (MK0), di mana tidak ada metakaolin tambahan yang ada dalam komposisi. Dalam kasus 10% MK, reaksi pozzolan menghasilkan lebih banyak produk hidrasi pada usia 28 hari, seperti dalam campuran dosis MK yang lebih tinggi, MK12.5 dan MK15. Fenomena ini dapat dijelaskan oleh efek pengenceran, yang berarti bahwa sehubungan dengan dosis MK yang lebih tinggi, dosis semen dalam komposisi lebih rendah, dan sebagai hasilnya, jumlah Portlandite yang lebih sedikit dihasilkan selama hidrasi. Akibatnya, membandingkan jumlah Portlandite dalam campuran yang mengandung MK, MK10 memiliki kandungan Portlandite yang tidak bereaksi lebih tinggi yang tersedia untuk reaksi pozzolan lebih lanjut, dan jumlah Portlandite yang lebih sedikit hadir dalam campuran MK12.5 dan MK15 untuk menginduksi reaksi pozzolan lebih lanjut. Namun, perbedaannya tidak terlalu signifikan antara sampel yang mengandung MK. Dalam kasus ketika 5% silika fume ditambahkan ke komposisi (MK10SF5), permukaan spesifik silika fume yang lebih tinggi memberikan permukaan reaksi yang lebih tinggi untuk reaksi kimia heterogen—inilah sebabnya derajat hidrasi lebih tinggi untuk campuran yang mengandung jumlah bahan tambahan yang sama (MK15). Derajat hidrasi yang lebih tinggi dicapai dalam campuran MK10SF5. Kita juga dapat menyatakan bahwa keberadaan dan jumlah bahan pelengkap, MK dan SF, tidak hanya memengaruhi derajat hidrasi, tetapi juga memiliki efek signifikan pada reologi campuran dalam keadaan segar. Di masa mendatang, kami berencana untuk mempelajari derajat hidrasi sebagai fungsi dari berbagai usia.
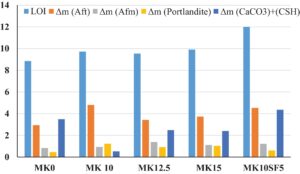
Mencicipi | Surat Keterangan | Δ m (Belakang) | Δm (Afm ) | Δ m (Portlandit) | Δm (CaCO3 ) + (CSH ) | Wb (% ) | sebuah (%) |
---|---|---|---|---|---|---|---|
MK0 | 8.85 | 2.93 | 0.83 | 0.44 | 3.49 | 5.63 | 23.46 |
MK10 | 9.72 | 4.80 | 0,93 | 1.23 | 0.53 | 7.49 | 31.21 |
MK12.5 | 9.54 | 3.42 | 1.38 | 0,91 | 2.48 | 6.73 | tanggal 28.04 |
MK15 | 9.90 | 3.72 | 1.12 | 1.03 | 2.41 | 6.86 | 28.58 |
MK10SF5 | 11.99 | 4.53 | 1.22 | 0,60 | 4.36 | 8.14 | 33.92 |
4 KESIMPULAN
Studi ini menguji pengaruh MK dan SF pada sifat 3DPC saat masih segar dan mengeras, termasuk kemampuan mengalir, kekuatan awal, kemampuan memompa, retensi bentuk, kemampuan membangun, kemampuan ekstrusi, kekuatan tekan, kekuatan ikatan antar lapisan, dan perilaku kimia pada suhu tinggi. Lima campuran diuji (MK0, MK10, MK12.5, MK15, dan MK10SF5), dan temuan-temuan utama dirangkum sebagai berikut:
- MK dan SF meningkatkan kekuatan awal, kemampuan membangun, dan retensi bentuk , dengan peningkatan optimal yang diamati pada 10%–12,5% MK. Namun, MK yang berlebihan (15%) mengurangi kemampuan pengerjaan, menyebabkan keretakan, dan mengganggu kontinuitas lapisan.
- Campuran MK10SF5 (10% MK + 5% SF) mencapai kinerja keseluruhan terbaik, dengan retensi bentuk yang sangat baik ( S 1 = 0,99), kemampuan bangun tertinggi (72 lapisan), kuat tekan (hingga 85,4 MPa pada spesimen cor), dan kekuatan ikatan antar lapisan (2,14 MPa), karena peningkatan kohesi, kerapatan pengepakan, dan reaktivitas pozzolan.
- Perilaku kompresif anisotropik diamati pada spesimen cetakan, dengan campuran MK10SF5 menunjukkan distribusi kekuatan paling seragam di semua arah, yang menunjukkan integritas struktural yang lebih baik.
- Analisis termogravimetri mengonfirmasi tingkat hidrasi yang lebih tinggi dalam MK10SF5 dibandingkan dengan MK0 dan MK15, menyoroti dampak positif ukuran partikel halus SF pada reaktivitas dan reologi keadaan segar.
- Campuran yang diusulkan menjanjikan untuk 3DCP skala besar , meskipun penelitian lebih lanjut direkomendasikan pada aspek daya tahan seperti karbonasi, serangan sulfat, masuknya klorida, dan ketahanan terhadap beku-cair.