Abstrak
Studi ini menyelidiki kelayakan pencetakan 3D beton ringan (LWC) yang menggabungkan manik-manik polistirena yang diperluas (EPS), dengan fokus pada pengoptimalan sifat mekanis dan kemampuan alir untuk pencetakan beton 3D (3DCP). Penelitian ini membahas kebutuhan akan material ringan yang dapat dicetak dan layak secara struktural dengan mengembangkan dan menguji campuran LWC yang dimodifikasi dengan manik-manik EPS, dievaluasi melalui uji standar ASTM untuk kekuatan tekan, kekuatan lentur, kemampuan alir, dan kemampuan cetak. Kepadatan yang dikeraskan berkisar antara 2213 hingga 752 kg/m 3 tercapai, dan hasilnya menunjukkan bahwa sementara EPS mengurangi kemampuan alir, penambahan superplasticizer memungkinkan peningkatan kemampuan cetak. Variasi dalam penggantian volume EPS mengungkapkan wawasan penting: penggantian di atas 60% menyebabkan penurunan substansial dalam kohesi pasta dan kemampuan alir, dengan volume EPS yang lebih tinggi (60%–70%) menyebabkan tekstur yang menggumpal dan kenyal dan menghasilkan kepadatan yang lebih rendah daripada air, membuat sampel mengapung. Campuran dengan volume EPS yang lebih tinggi menunjukkan perilaku yang lebih lentur dan penyerapan energi yang stabil tanpa kegagalan mendadak, meskipun dengan mengorbankan kekuatan tekan, yang turun menjadi 4,2 MPa untuk 50% EPS—penurunan yang signifikan dari 23,6 MPa pada beton standar. Meskipun dapat dicetak hingga 50% EPS, campuran ini memerlukan pengoptimalan lebih lanjut untuk aplikasi struktural umum, memposisikan LWC berbasis EPS sebagai material yang menjanjikan untuk penggunaan 3DCP tertentu.
1. PENDAHULUAN
Industri konstruksi tengah mengalami transformasi besar dengan penerapan pencetakan beton 3D (3DCP), sebuah teknologi yang secara substansial memangkas waktu konstruksi dan meminimalkan kebutuhan tenaga kerja. Kemajuan ini mengurangi limbah, memungkinkan desain yang kompleks dan dapat disesuaikan, serta menyediakan pendekatan yang cepat dan efisien untuk mengatasi permintaan perumahan yang terus meningkat. Melalui proses otomatis, 3DCP mendukung praktik konstruksi yang dapat diskalakan dan berkelanjutan, menjadikannya solusi yang layak untuk mengatasi kekurangan perumahan.
Sejumlah penelitian juga mengeksplorasi penggunaan beton ringan (LWC) dalam 3DCP untuk lebih meningkatkan efisiensi material dan memenuhi persyaratan struktural dalam berbagai aplikasi. Bumanis dkk. 1 meneliti potensi pencetakan 3D dengan komposit gipsum ringan yang menggabungkan manik-manik EPS untuk menghasilkan komponen bangunan yang ringan, bersifat isolasi termal dan akustik. Penelitian ini menemukan bahwa meskipun pencetakan 3D mengurangi kekuatan tekan dan lentur komposit EPS–gipsum, penyesuaian rasio air terhadap gipsum meningkatkan homogenitas material dan keseragaman struktural. Penelitian lain mengevaluasi lima campuran LWC dengan pasir ceramsite untuk pencetakan 3D struktur berongga, menemukan bahwa desain kisi persegi panjang memberikan ketahanan tekan terbaik dan struktur rangka unggul dalam kekuatan lentur, dengan distribusi tegangan dianalisis melalui metode elemen diskrit. 2
Dalam beberapa tahun terakhir, material LWC yang mengandung bahan baku berkelanjutan semakin diminati karena beberapa sifat yang diinginkan. LWC menawarkan berbagai manfaat, seperti isolasi termal yang lebih baik, kepadatan yang lebih rendah, penyerapan energi yang lebih tinggi, dan daur ulang bahan limbah dalam konstruksi. LWC diproduksi dengan mengganti sebagian agregat alami dengan agregat yang lebih ringan yang dapat diperoleh secara alami (batu apung, diatomit, dan perlit) atau secara sintetis, misalnya, EPS .
Karena kepadatannya yang rendah dan penggunaan yang luas dalam sistem isolasi dan pengemasan, EPS merupakan material yang cocok sebagai agregat ringan, dengan kepadatan berkisar antara 10 hingga 30 kg/m 3 , yang jika dibandingkan dengan kepadatan agregat alami (1200–1750 kg/m 3 ) adalah sekitar 1% dari kepadatan agregat alami. 5 EPS sel tertutup mengandung 98% udara dan 2% polistirena, dan memiliki daya serap air yang lebih rendah daripada agregat alami. 6 Menggunakan manik-manik EPS dalam beton menawarkan kesempatan untuk mencegah tantangan lingkungan dari pembuangan dan daur ulang material ini (EPS) karena masalah yang terkait dengan komposisi kimianya yang dapat menunda kerusakannya hingga berabad-abad jika dikubur di tempat pembuangan sampah. 7 Pada tahun 2000, dilaporkan bahwa AS menggunakan sekitar 722.000 ton polistirena kemasan makanan bekas (yaitu, daur ulang), yang berpotensi untuk digunakan sebagai agregat ringan dalam beton. 8 Selain itu, limbah polistirena dapat dimanfaatkan sebagai sumber produksi EPS yang dapat digunakan dalam beton dan menghindari proses pembuangan mahal yang dipersyaratkan oleh peraturan lingkungan dan ekosistem internasional.
Panel dinding sandwich beton, 6 blok beton penahan beban, 5 pembatas jalan beton, 9 dinding gorden, sistem lantai komposit, struktur laut terapung ringan, lapisan pelindung untuk struktur, 10 dan bata ringan 11 merupakan aplikasi penting dari beton EPS. Kelemahan utama EPS adalah kuat tekan yang lebih rendah, laju penyusutan yang lebih tinggi, creep yang lebih besar, dan ketahanan korosi yang lebih rendah. 12 Penyusutan pengeringan beton EPS lebih besar daripada beton konvensional karena kekakuan dan kuat tekan yang lebih rendah (yaitu, ketahanan yang lebih rendah terhadap penyusutan), yang sebagian dapat dinetralisir oleh aditif atau serat. 13 Kelemahan beton EPS sebagian dapat dikompensasi oleh perlakuan termal pada manik-manik. 14
Mengganti agregat alami dengan manik-manik EPS dalam beton mengubah perilaku tegangan-regangan beton secara mendasar. Perilaku getas beton berubah menjadi perilaku yang lebih daktail dengan disipasi energi yang lebih tinggi dan kegagalan bertahap. 15 , 16 Menurut hasil pengujian, 13 mengganti 30% agregat dengan EPS menyebabkan pengurangan kemerosotan hingga 85%. Lebih jauh lagi, secara umum, peningkatan volume EPS dalam beton menurunkan nilai permeabilitas klorida, yang dapat melindungi tulangan yang tertanam dalam beton. Dilaporkan juga bahwa beton EPS memiliki daya tahan yang lebih baik terhadap serangan kimia karena perilaku inert agregat EPS. 17 Di sisi lain, mode kegagalan beton EPS terkait dengan fraksi volume EPS; semakin tinggi kandungannya, semakin baik deformasi plastiknya. Hubungan antara kuat tekan dan fraksi volume beton EPS menunjukkan kemiripan yang dekat dengan peluruhan eksponensial.
Campuran serbaguna telah dipelajari dengan EPS untuk mencapai sifat-sifat tertentu untuk berbagai aplikasi. Resin epoksi, epoksi yang diemulsi air, abu terbang, silika mikro, dan agen pengikat lainnya telah diteliti untuk mencegah segregasi dan meningkatkan beton EPS. 13 Berdasarkan penelitian sebelumnya, butiran EPS halus hanya digunakan untuk mencapai kekuatan yang lebih tinggi dengan fraksi volume yang sama. 18 – 20 Butiran EPS berukuran lebih kecil menghasilkan kekuatan tekan 20 dan tarik 21 yang lebih tinggi dibandingkan dengan fraksi volume EPS yang sama dengan butiran berukuran lebih besar.
Karena kepadatan EPS yang sangat ringan, beton agregat ringan rentan terhadap segregasi selama pencampuran. Karena EPS adalah sel tertutup yang terbuat dari polistirena dan udara, ia mengapung di permukaan selama prosedur pencampuran dan perlu dicampur dengan instruksi khusus untuk mendapatkan campuran yang seragam tanpa segregasi apa pun. Babu dan Babu 22 menambahkan asap silika halus untuk meningkatkan ikatan antara manik-manik EPS dan pasta semen. Xu et al. 5 menerapkan lateks karet stirena-butadiena (SBR) untuk meningkatkan ikatan EPS dan beton untuk meningkatkan kekuatan beton. Aditif ikatan seperti resin epoksi (dispersi berair polivinil propionat), epoksi yang diemulsi air, dan partikel EPS yang diolah secara kimia seperti BST digunakan untuk meningkatkan kekuatan ikatan antarmuka antara manik-manik dan matriks. Dilaporkan bahwa campuran mineral seperti abu terbang, asap silika, dan abu sekam padi digunakan sebagai aditif pengikat untuk meningkatkan kekuatan ikatan antarmuka antara butiran dan matriks serta meningkatkan dispersi butiran EPS dalam matriks semen. 17 Pencampuran EPS dengan matriks semen perlu dipertimbangkan untuk mencegah segregasi agregat LWC. Oleh karena itu, penelitian menggarisbawahi proses pencampurannya. Pencampuran kering butiran EPS dan matriks semen dengan penambahan air secara bertahap selama pencampuran berhasil dilakukan. 23 Metode lain awalnya membasahi butiran EPS dengan proporsi campuran air dan superplasticizer. 22
Untuk menyelidiki sifat-sifat beton dengan persentase EPS yang bervariasi, penelitian ini melakukan uji eksperimental terhadap sifat-sifat mekanis, kemampuan mengalir, dan kemampuan cetak material. Uji kemampuan mengalir dimaksudkan untuk mengevaluasi kemampuan beton untuk mengalir secara merata melalui nosel pencetak. Terakhir, uji kemampuan cetak dilakukan untuk memeriksa kemampuan material untuk diekstrusi lapis demi lapis tanpa mengempis atau kehilangan bentuknya. Tujuan dari pelaksanaan uji ini adalah untuk menentukan rasio campuran EPS dan bahan-bahan lain yang optimal untuk 3DCP, yang akan berkontribusi pada pengembangan proses pencetakan 3D yang efisien dan efektif untuk struktur beton.
2 PENELITIAN EKSPERIMENTAL
2.1 Bahan dan proporsi campuran
Untuk studi ini, beton kontrol dikembangkan dengan menggunakan Gulf Concrete Technologies (GCT) khusus untuk 3DCP. Komposisi GCT disajikan dalam Tabel 1 , dengan batas ukuran partikel campuran kering 1 mm dan kepadatan kering 1457,7 kg/m 3 . Untuk mencegah akumulasi butiran EPS di dalam pompa, ukuran butiran EPS yang digunakan dibatasi hingga kurang dari 1 mm. Ukuran ini dipilih karena keterbatasan pencetakan dan kemungkinan kekuatan yang lebih tinggi daripada ukuran butiran yang lebih besar pada beton EPS. Sifat-sifat EPS yang digunakan dalam studi ini tercantum dalam Tabel 2 .
Nama kimia komponen |
Batu kapur yang dihaluskan |
kapur sirih |
Silika kristal |
Semen Portland |
Semen kalsium sulfoaluminat |
Selulosa |
Catatan : Pati.
Berat jenis | 0,033 |
Kepadatan massal | 17,62 kg/ m3 |
Diameter manik-manik | 0,8–1 milimeter |
Tabel 3 menunjukkan dua set campuran yang digunakan dalam studi yang disajikan dalam makalah ini. Dalam campuran tipe-Z, sebagian GCT diganti dengan EPS, yang mengurangi daya alir beton, sehingga memerlukan penambahan superplasticizer untuk mempertahankan daya alir yang memuaskan. Ditetapkan bahwa daya alir GCT harus berada dalam diameter antara 22 dan 25 cm dalam uji tabel alir agar dapat dicetak berdasarkan pengalaman pencetakan sebelumnya. Hasilnya, campuran tipe-M merupakan versi modifikasi dari tipe-Z dengan superplasticizer berbasis polikarboksilat tambahan.
Mencicipi | Hasil per saham (%) | TKG (kg/ m3 ) | Air (kg/ m3 ) | Berat jenis partikel (kg/ m3 ) | Superplasticizer (kg/ m3 ) |
---|---|---|---|---|---|
M0 | 0.0 | 1792.5 | 358.5 | 0.0 | 5.0 |
Bahasa Indonesia: M1 | 10.0 | 1579.9 | 316.0 | 2.8 | 15.6 |
M2 | 20.0 | 1403.2 | 280.6 | 5.6 | 14.4 |
M3 | 30.0 | 1245.4 | 249.1 | 8.5 | 13.4 |
M4 | 40.0 | 1104.4 | 220.9 | 11.8 | 12.5 |
M5 | 50.0 | 977.9 | 195.6 | 15.7 | 11.9 |
M6 | 60.0 | 863.8 | 172.8 | 19.8 | 11.7 |
M7 | 70.0 | 759.3 | 151.9 | 22.4 | 11.9 |
Z0 | 0.0 | 1828.4 | 365.7 | 0.0 | 0.0 |
Z1 | 10.0 | 1640.8 | 328.2 | 2.9 | 0.0 |
Z2 | 20.0 | 1471.7 | 294.3 | 5.9 | 0.0 |
Z3 | 30.0 | 1294.2 | 258.8 | 8.9 | 0.0 |
Z4 | 40.0 | 1159.3 | 231.9 | 12.4 | 0.0 |
Z5 | 50.0 | 1017.4 | 203.5 | 16.3 | 0.0 |
Z6 | 60.0 | 908.3 | 181.7 | 19.5 | 0.0 |
Z7 | 70.0 | 790.1 | 158.0 | 21.8 | 0.0 |
Telah ditetapkan bahwa ukuran partikel maksimum dalam campuran kering tidak boleh melebihi 1 mm untuk mencegah penyumbatan pada pompa dan menghindari potensi kerusakan pada peralatan. Selain itu, peningkatan ukuran partikel dapat menyebabkan komplikasi pada stator printer. Akibatnya, baik EPS yang digunakan dalam pengecoran maupun pencetakan harus melekat pada diameter maksimum 1 mm, dengan diameter minimum 0,8 mm.
2.2 Persiapan dan pengujian spesimen
Karena risiko segregasi, diperlukan kehati-hatian khusus saat mencampur EPS dengan mortar, yang berbeda dari prosedur pencampuran beton konvensional. Awalnya, air ditambahkan secara bertahap ke GCT sambil mencampur hingga mortar menjadi seragam. Selanjutnya, EPS ditambahkan secara bertahap, dan pencampuran dilanjutkan setidaknya selama 1 menit hingga manik-manik terdistribusi secara merata. Selain itu, ditemukan bahwa menambahkan EPS ke campuran kering sebelum mencampur dengan air menghasilkan distribusi EPS yang seragam dalam campuran akhir, yang lebih cocok untuk pencetakan 3D. Gambar 1 menunjukkan dua penampang balok setelah uji lentur. Jelas dari gambar bahwa persentase EPS di area yang ditunjukkan tidak konsisten, dan distribusi agregat ringan tidak seragam. Variasi ini dapat dianggap cacat selama pengujian sifat mekanis. Sampel dengan persentase EPS yang tinggi menunjukkan distribusi agregat ringan yang lebih seragam daripada sampel dengan persentase EPS sedang.

Sampel tipe Z menjalani fase pengujian, yang mencakup uji alir untuk menentukan kesesuaiannya untuk dicetak. Beberapa sampel memerlukan modifikasi dengan superplasticizer agar berada dalam rentang pencetakan yang tepat. Sampel yang dimodifikasi selanjutnya diklasifikasikan ulang sebagai campuran tipe M, yang menunjukkan bahwa sampel tersebut sekarang cocok untuk dicetak. Uji tabel alir dilakukan untuk mengevaluasi alir campuran berdasarkan ASTM C1437. 24 Uji ASTM C1437, atau uji Aliran Mortar Semen Hidrolik, mengukur kemampuan kerja mortar semen dengan mengamati seberapa banyak sampel mortar menyebar saat dilepaskan dari cetakan alir dan dikenai 25 tetes pada meja logam. Untuk pengulangan, tiga pengujian dilakukan pada kumpulan material yang sama di lingkungan yang sama dalam area pencetakan dengan suhu dan kelembapan yang sama. Kepadatan campuran segar dan mengeras diperoleh berdasarkan ASTM C138 25 dan ASTM C642. 26 Uji kepadatan segar ASTM C138 mengukur massa beton yang baru dicampur dalam wadah dengan volume yang diketahui, kemudian menghitung kepadatan dengan membagi massa dengan volume. ASTM C642 untuk kepadatan yang mengeras melibatkan pengeringan sampel, merendamnya dalam air hingga jenuh, dan mengukur beratnya di dalam air dan di udara, yang memungkinkan perhitungan kepadatan berdasarkan perpindahan air. Sampel kubus cor tipe Z dan M menjalani uji tekan menurut ASTM C109. 26 ASTM C109 mengukur kekuatan tekan mortar semen hidrolik menggunakan spesimen kubus 50 mm (2 inci). Mortar dicampur dan dicetak menjadi bentuk kubus, diawetkan dalam kondisi terkendali, dan kemudian dikenakan gaya tekan yang meningkat dalam mesin uji hingga rusak. Hanya sampel tipe M cor yang diuji untuk kekuatan lentur menggunakan balok beton sederhana berdasarkan ASTM C78. ASTM C78 menentukan kekuatan lentur beton dengan menguji balok beton sederhana di bawah metode pembebanan titik ketiga. Dimensi balok yang digunakan pada pengujian adalah lebar 8 cm, kedalaman 8 cm, dan panjang 24 cm (Gambar 2 ) .
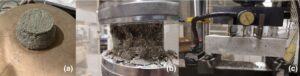
Pengujian dilakukan berdasarkan ASTM pada sampel beton cor untuk mengukur sifat beton EPS guna menilai kualitas bagian cetakan. Sampel tipe-M merupakan sampel yang ditujukan untuk bagian 3DCP dari penelitian ini dengan superplasticizer yang disesuaikan. Oleh karena itu, kualitas sampel tipe-M yang dicetak dinilai untuk dibandingkan dengan GCT sebagai beton kontrol dari penelitian ini.
3 HASIL DAN PEMBAHASAN
3.1 Tabel aliran
Kemampuan alir sampel seri-M dan seri-Z diuji menggunakan uji tabel alir untuk mengukur kemampuan cetaknya. Saat fraksi volume EPS dalam campuran meningkat, diameter kemampuan alir sampel tipe-Z menurun (Gambar 3 ). Simpangan baku ditampilkan dalam gambar untuk menunjukkan keakuratan dan variabilitas hasil untuk setiap sampel, berdasarkan data dari tiga spesimen. Saat 10% EPS ditambahkan ke campuran beton, diameter kemampuan alir beton tipe-M menurun sekitar 1,2%, sedangkan beton tipe-Z menurun sekitar 3,5%. Demikian pula, saat 20% EPS ditambahkan, diameter kemampuan alir beton tipe-M menurun sekitar 2,8%, sedangkan beton tipe-Z menurun sekitar 4,8%.
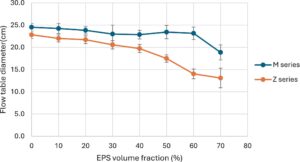
Selama pengujian, diamati bahwa ketika fraksi volume EPS mencapai 60%, pasta yang tersedia tidak cukup untuk membungkus manik-manik sepenuhnya. Sampel seri M menunjukkan kemampuan alir yang lebih tinggi karena dosis superplasticizer yang lebih tinggi yang ditambahkan ke campuran beton. Selama pengujian, juga diamati bahwa dalam sampel 60% dan 70%, pasta tidak sepenuhnya membungkus manik-manik EPS, dan beberapa manik-manik EPS terguling keluar selama operasi uji tabel alir. Temuan penelitian menunjukkan bahwa fraksi volume EPS secara signifikan mempengaruhi diameter kemampuan alir, dengan pengurangan yang lebih tinggi diamati pada fraksi volume yang lebih tinggi. Berdasarkan temuan tersebut, tampaknya sampel M6 memiliki fraksi volume EPS yang dapat dicetak tertinggi.
3.2 Kepadatan
Kepadatan segar sampel tipe-M berkurang dari 2171 menjadi 950 kg/m 3 , sedangkan kepadatan segar sampel tipe-Z sedikit lebih kecil daripada kepadatan untuk tipe-M. Pada sampel yang mengandung persentase EPS yang lebih tinggi, ekspansi diamati setelah 2–3 jam pengecoran. Jumlah ekspansi lebih tinggi pada spesimen tipe-M, dengan ekspansi maksimum 3 mm di tengah cetakan balok, dan menyebabkan retak permukaan pada sampel (Gambar 4 ). Ekspansi ini hanya diamati pada sampel yang mengandung EPS, dan ekspansi lebih tinggi pada sampel dengan jumlah EPS yang lebih tinggi. Ada sedikit perbedaan antara kepadatan sampel tipe-M dan Z yang mengandung lebih dari 30% EPS, yang dapat dikaitkan dengan superplasticizer (Gambar 6 ). Pengurangan kepadatan yang dicapai melalui penggunaan EPS dalam beton merupakan faktor penting untuk struktur 3DCP, karena dapat secara signifikan mengurangi berat komponen yang dicetak. Studi kami menyelidiki dampak EPS pada kepadatan beton, dengan hasil yang menunjukkan penurunan substansial dalam kepadatan yang diperkeras dari 1882,6 menjadi 895,0 saat fraksi volume EPS meningkat dari 0% menjadi 70% dalam sampel tipe-M. Data tersebut mengungkapkan penurunan kepadatan yang konsisten saat fraksi volume EPS meningkat, dengan pengurangan terbesar terjadi antara fraksi volume 0% dan 20%. Pada fraksi volume 20%, kepadatan yang diperkeras menurun sekitar 28% dibandingkan dengan sampel kontrol tanpa EPS. Namun, di atas fraksi volume 50%, laju pengurangan kepadatan melambat tetapi tetap signifikan. Secara keseluruhan, temuan studi ini menunjukkan bahwa pengurangan kepadatan yang dicapai melalui penggunaan EPS dalam beton merupakan faktor penting untuk menciptakan struktur 3DCP yang ringan. Hasilnya memberikan wawasan berharga tentang potensi manfaat dari penggabungan EPS dalam beton, dan penelitian lebih lanjut diperlukan untuk mengoptimalkan fraksi volume EPS untuk berbagai aplikasi.
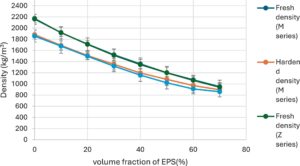
3.3 Kekuatan tekan
Penambahan butiran EPS ke beton dapat berdampak signifikan pada kekuatan tekannya. Seiring dengan meningkatnya fraksi volume butiran EPS dalam campuran beton, kekuatan tekan material cenderung menurun. Hal ini karena butiran EPS memiliki kekuatan yang dapat diabaikan dibandingkan dengan agregat tradisional seperti pasir dan kerikil, dan keberadaannya dalam beton mengurangi area efektif yang menahan beban. Tingkat hal ini akan bergantung pada sifat khusus campuran beton dan jumlah serta ukuran butiran EPS yang digunakan. Jika butiran EPS tidak terdistribusi secara merata dalam campuran beton, butiran tersebut dapat membentuk gugusan di area tertentu, yang menyebabkan cacat pada material yang selanjutnya dapat mengurangi kekuatannya.
Gambar 5 dan 6 mengilustrasikan perkembangan kuat tekan sampel beton EPS tipe M dan Z selama 7, 28, dan 90 hari. Kuat tekan sampel beton EPS yang mengandung berbagai persentase butiran EPS diselidiki setelah 28 hari perawatan. Hasilnya menunjukkan tren yang jelas dari penurunan kuat tekan dengan peningkatan fraksi volume EPS. Pada 0% EPS dalam sampel tipe M, kuat tekan adalah 23,6 MPa, sedangkan pada 70% EPS, kekuatannya turun menjadi 1,5 MPa. Secara khusus, kuat tekan menurun dari 22,1 MPa pada 10% EPS menjadi 8,6 MPa pada 40% EPS, dan kemudian menjadi 4,2 MPa pada 50% EPS. Kekuatan terendah diamati pada sampel dengan 70% EPS, yang hanya 6,4% dari kekuatan sampel dengan 0% EPS. Hasil ini menunjukkan bahwa menambahkan butiran EPS dalam beton dapat secara signifikan mengurangi kuat tekannya, yang harus dipertimbangkan saat merancang struktur beton EPS.
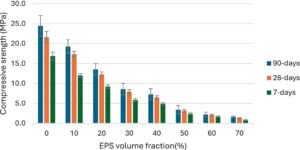
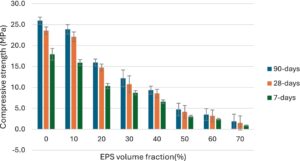
Kekuatan tekan beton tipe-M dinilai pada durasi perawatan 7, 28, dan 90 hari, menggunakan proporsi EPS yang berbeda mulai dari 0% hingga 70%. Kekuatan pada 28 hari berkisar antara 23,6 hingga 1,5 MPa, yang menunjukkan penurunan kekuatan dengan peningkatan kandungan EPS. Pada 90 hari, kekuatan tekan berkisar antara 25,9 hingga 1,9 MPa, yang menunjukkan tren yang sama dengan penurunan kekuatan saat kandungan EPS meningkat. Khususnya, kekuatan yang hilang signifikan pada sampel 90 hari dan 28 hari. Hasilnya menunjukkan bahwa penambahan EPS dapat memiliki efek yang merugikan pada kekuatan tekan beton tipe-M dari waktu ke waktu.
Dibandingkan dengan sampel tipe-M, sampel tipe-Z secara umum menunjukkan nilai kuat tekan yang lebih rendah pada sampel umur 90 dan 28 hari. Pada umur 28 hari, nilai kuat tekan tertinggi untuk sampel tipe-Z adalah 21,6 MPa pada 0% EPS, yang sedikit lebih rendah daripada nilai kuat tekan tertinggi sampel tipe-M pada 23,6 MPa. Namun, penurunan kekuatan dengan meningkatnya kandungan EPS lebih jelas terlihat pada sampel tipe-M. Misalnya, kekuatan sampel tipe-Z turun menjadi 1,3 MPa pada 70% EPS, yang lebih rendah daripada nilai yang sesuai dari sampel tipe-M pada 1,5 MPa. Sampel tipe-Z menunjukkan tren yang sama dengan sampel tipe-M, di mana kuat tekan menurun dengan meningkatnya fraksi volume EPS, dan penurunan lebih signifikan pada kandungan EPS yang lebih tinggi. Hasil-hasil ini menyoroti pentingnya mempertimbangkan jenis beton EPS yang digunakan, karena dapat memengaruhi sifat kuat tekan material. Model prediksi untuk sampel tipe M diperoleh dengan menggunakan regresi eksponensial, dan menggunakan persamaan eksponensial
untuk memprediksi kekuatan tekan sampel beton EPS pada umur 28 hari, berdasarkan persentase EPS.
3.4 Kekuatan lentur
Gambar 2c menggambarkan pengaturan pengujian yang ditentukan oleh ASTM C78 untuk mengukur modulus pecah (MOR) sampel beton di bawah tekukan empat titik. Gambar 7 juga mengilustrasikan bagaimana penambahan fraksi volume EPS memengaruhi nilai MOR. MOR menurun saat fraksi volume EPS meningkat. Hubungan ini dapat diamati melalui analisis regresi eksponensial, yang menunjukkan korelasi negatif yang jelas antara kedua variabel. Pada 0% EPS, MOR adalah 3,52 MPa, sedangkan pada 70% EPS, MOR turun menjadi 0,25 MPa. Pengurangan MOR saat fraksi volume EPS meningkat dapat dikaitkan dengan pembentukan rongga di dalam material karena adanya manik-manik EPS. Rongga ini membatasi luas permukaan yang tersedia bagi material untuk menahan gaya tekuk, yang mengakibatkan penurunan kekuatan keseluruhan.
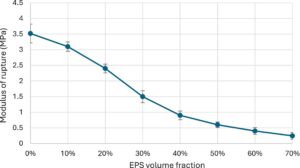
Selain itu, ikatan yang lebih lemah antara EPS dan pasta beton berkontribusi pada kekuatan tarik yang lebih rendah dalam beton, yang pada akhirnya menyebabkan penurunan yang signifikan dalam kekuatan lentur ultimit. Lokasi kegagalan untuk semua sampel diamati berada di sepertiga tengah bagian, yang menunjukkan bahwa tegangan tarik di bagian bawah balok melebihi kekuatan tariknya. Persamaan regresi eksponensial (Persamaan ( 1 )) dapat digunakan untuk menggambarkan korelasi antara modulus pecah dan fraksi volume manik-manik EPS. Persamaan ini diturunkan dengan melakukan analisis regresi eksponensial pada data yang disajikan dalam Gambar 8. Oleh karena itu, jumlah EPS yang digunakan dalam campuran beton sangat penting karena secara signifikan mempengaruhi kekuatan tarik dan lentur material. Ini sangat penting untuk dinding pencetakan beton 3D karena mungkin tidak diperkuat dengan benar atau memadai seperti beton bertulang konvensional. Dinding ini dapat mengalami berbagai jenis efek beban, seperti geser, lentur, atau tekuk yang disebabkan oleh beban eksternal karena angin dan/atau gempa bumi. Oleh karena itu, tidak seperti struktur beton bertulang konvensional, penting untuk mengetahui potensi kurangnya penguatan yang tepat dalam sistem ini.
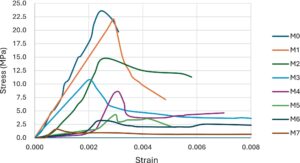
3.5 Ketangguhan
Gambar 8 menggambarkan perilaku tegangan-regangan beton EPS dan diperoleh melalui uji kompresif sampel tipe-M. Memahami kurva tegangan-regangan sangat penting untuk menentukan faktor-faktor yang menentukan perilaku mekanis suatu material. Berbeda dengan beton konvensional, beton EPS menunjukkan penyerapan energi dan perilaku ketangguhan yang berbeda. Hal ini karena perilaku getas beton berubah menjadi perilaku daktail dengan deformasi yang lebih signifikan sebelum terjadi kegagalan. Awalnya, kurva tegangan-regangan beton EPS menunjukkan peningkatan tegangan secara bertahap, yang sesuai dengan regangan substansial yang disebabkan oleh pemadatan manik-manik berongga EPS.
Bentuk kurva awalnya tampak linier, dengan tegangan dan regangan menunjukkan hubungan yang proporsional. Namun, setelah melewati titik tertentu, respons tegangan-regangan menjadi nonlinier, yang menyebabkan peningkatan tegangan dengan setiap peningkatan regangan secara bertahap, yang akhirnya mengarah pada kekuatan akhirnya. Selain itu, beton EPS menunjukkan penyerapan energi yang tinggi karena sifatnya yang daktail, yang memungkinkannya menahan lebih banyak deformasi dan tegangan sebelum mengalami kegagalan. Beton EPS yang mengandung lebih dari 50% butiran EPS menunjukkan perilaku unik dalam kurva tegangan-regangan.
Selain puncak awal yang diamati pada beton konvensional, puncak kedua terlihat pada regangan yang lebih tinggi pada sampel yang mengandung EPS. Kontras puncak kedua pada M4, M5, dan M6 lebih jelas, dengan puncak kedua M4 mencapai 61,5% dari puncak pertama dan M5 mencapai 60,9%. Sampel M7 menunjukkan tingkat fleksibilitas yang tinggi, sehingga tidak rusak bahkan ketika mesin mencapai lendutan maksimum yang dapat diterapkan pada sampel. Lebih jauh, Sampel M7 tidak menunjukkan puncak tegangan kedua, dan setelah puncak pertama, tegangan menurun menjadi 0,7 MPa sambil terus mengalami lendutan.
3.6 Pencetakan 3D beton EPS
Menurut uji tabel alir, sampel tipe Z dapat dicetak dengan EPS hingga 20% (Z2), sedangkan sampel tipe M dapat dicetak dengan EPS hingga 60% (M6). Namun, upaya untuk mencetak M6 tidak berhasil karena partikel EPS tidak terdistribusi dengan baik dalam pasta, sehingga terjadi segregasi selama proses pemompaan dan hasil cetak akhir yang heterogen. Selama uji coba dengan senapan mortar, kualitas kemampuan cetak material diuji untuk mengevaluasi kemampuan ekstrusinya dan untuk menentukan hasil uji tabel alir. Hasil uji menunjukkan bahwa semua sampel, kecuali M6 dan M7, dapat dicetak. Namun, hasil uji tabel alir M6 berada dalam kisaran pencetakan berdasarkan pengalaman sebelumnya. Gambar 9 menunjukkan sampel yang dicetak dengan senapan mortar.
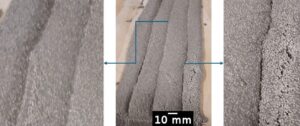
Setelah melakukan pengujian yang dibahas, menggabungkan EPS ke dalam beton menawarkan beberapa keuntungan dan kerugian. Jumlah EPS yang tepat untuk ditambahkan ke elemen cetak harus ditentukan berdasarkan sifat-sifat khusus yang dibutuhkan untuk setiap aplikasi. Tabel 4 menyajikan hasil pengujian sebelumnya yang dapat membantu menentukan fraksi volume EPS dalam beton. Kepadatan beton yang dikeraskan menurun hingga 46% untuk M4 dan terus menurun pada M5, M6, dan M7. Uji tekan menunjukkan penurunan kekuatan yang cepat setelah M4, dengan penurunan kekuatan M4 sebesar 50%.
Mencicipi | Persentase EPS | Kepadatan | Kekuatan | Kemampuan mengalir | LEBIH BANYAK | Dapat dicetak |
---|---|---|---|---|---|---|
M0 | 0% | 100% | 100% | 100% | 100% | Ya |
Bahasa Indonesia: M1 | 10% | 90% | 94% | 99% | 88% | Ya |
M2 | 20% | 80% | 63% | 97% | 68% | Ya |
M3 | 30% | 72% | 46% | 94% | 43% | Ya |
M4 | 40% | 64% | 36% | 93% | 26% | Ya |
M5 | 50% | 57% | 18% | 96% | 17% | Ya |
M6 | 60% | 52% | 14% | 95% | 11% | TIDAK |
M7 | 70% | 48% | 6% | 77% | 7% | TIDAK |
a Semua persentase berkenaan dengan kasus M0 (tanpa EPS).
Selain itu, kekuatan M4 kira-kira dua kali lipat dari M5, tetapi kepadatannya menurun hingga 7%. Uji alir menunjukkan bahwa hanya sampel M7 yang tidak berada dalam kisaran kemampuan cetak, tetapi uji cetak dengan pistol mortar menunjukkan bahwa M6 juga tidak dapat dicetak. MOR secara konsisten menurun dengan peningkatan fraksi volume EPS tanpa penurunan yang tiba-tiba.
Hasilnya ditunjukkan pada Tabel 4 , yang menunjukkan bahwa M5 adalah sampel yang dapat dicetak dengan persentase EPS tertinggi. Kepadatan M5 yang dikeraskan adalah 1081 kg/m 3 , yang cukup rendah untuk mencapai LWC yang diinginkan. Kekuatan tekan M5 adalah 3,2 MPa setelah 28 hari dan 3,4 MPa setelah 90 hari, meskipun kehilangan kekuatan sampel M5 28 dan 90 hari dibandingkan dengan sampel M4 signifikan dan menjadikan M4 pilihan yang lebih disukai. M4 dan M5 menunjukkan perilaku tegangan dan regangan yang serupa dengan toleransi lendutan yang tinggi.
Latihan pencetakan utama dilakukan oleh lengan robot industri 6-sumbu ABB IRB 6640-235, untuk memandu nosel ekstruder di sepanjang lintasan alat yang dihasilkan dan mencetak komponen. Mixer dan pompa M-tec Duomix 2000 digunakan untuk mencampur campuran kering dengan air dan kemudian mengekstruksi (Gambar 10 ). Hanya M0, M1, dan M4 yang dicetak menggunakan metode ini.
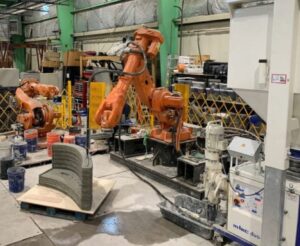
Gambar 11 menunjukkan kemampuan cetak M0 dan M1; bagian yang dicetak memiliki distribusi EPS yang homogen dan stabilitas tahap awal yang cukup untuk menoleransi filamen atas. Properti yang dibutuhkan dan aplikasi elemen cetak 3D menentukan desain campuran yang tepat. Proses pencetakan untuk M6 dan M7 tidak berhasil, karena jumlah EPS yang berlebihan menyebabkan akumulasinya di stator. Pada saat yang sama, kepadatan rendah dan kompatibilitas tinggi material mengakibatkan masalah. Akibatnya, plastik yang mengelilingi stator terdorong tanpa ekstrusi yang tepat, menyebabkan stator menjadi terlalu panas. Diameter nosel pencetakan adalah 25 mm, dan filamen yang dicetak berbentuk persegi panjang, dengan dimensi tinggi 18 mm dan lebar 27 mm. Kecepatan cetak nosel pada bidang X – Y diatur ke 2 cm/s. Objek cetak yang digunakan untuk mengevaluasi kemampuan cetak campuran terdiri dari tiga lingkaran, masing-masing dengan diameter 25 cm, dan lebar cetak yang terdiri dari dua lapisan dengan total 54 mm. Desain ini mempertimbangkan kekuatan luluh awal material untuk memastikan bahwa deformasi apa pun pada lapisan bawah tidak mengganggu stabilitas struktur.
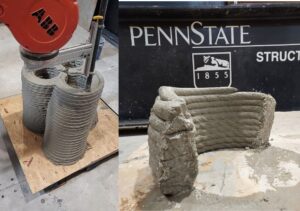
Gambar 12 mengilustrasikan hubungan antara kekuatan dan kepadatan untuk menilai campuran. Untuk berbagai aplikasi komponen cetak, kepadatan minimum yang memenuhi kekuatan yang dibutuhkan dapat dipilih untuk memanfaatkan manfaat kepadatan yang lebih rendah. Bergantung pada apakah komponen tersebut ditujukan untuk penggunaan struktural atau non-struktural, jumlah EPS yang tepat dapat dimasukkan. Kandungan EPS yang lebih tinggi memberikan isolasi termal yang lebih baik, yang memerlukan penyelidikan lebih lanjut.
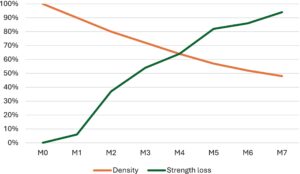
Pencetakan dengan EPS menghadirkan tantangan bagi sistem pemompaan karena kompresibilitas butiran EPS dan gesekan yang ditimbulkannya, yang memengaruhi reologi beton. Bergantung pada jenis pompa dan panjang selang, campuran mungkin memerlukan penyesuaian dan pelumas pompa tambahan untuk mencegah pompa atau stator terlalu panas selama pemompaan. Tantangan ini menjadi lebih jelas dengan komponen yang lebih besar dan kandungan EPS yang lebih tinggi, yang semakin mempersulit proses pemompaan.
4 KESIMPULAN
Studi ini menyajikan penyelidikan awal tentang dampak butiran EPS pada sifat beton yang digunakan dalam pencetakan 3D. Studi ini meneliti efek butiran EPS pada kemampuan mengalir, kemampuan cetak, kekuatan tekan, kekuatan lentur, dan kepadatan beton yang dihasilkan. Studi ini meneliti dua jenis beton EPS. Temuan menunjukkan bahwa penambahan butiran EPS dapat memiliki pengaruh yang signifikan pada sifat material beton. Poin-poin penting dalam kesimpulan adalah sebagai berikut:
- Penambahan butiran EPS ke dalam campuran beton secara signifikan mengurangi kepadatan segar dan keras dari sampel yang dimodifikasi (tipe M) dan tidak dimodifikasi (tipe Z), dengan kepadatan segar dari sampel tipe M berkurang dari 2171 menjadi 950,4 kg/m3 dan sampel tipe Z berkurang dari 2161 menjadi 940 kg/ m3 . Perbedaan antara kepadatan keras dan kepadatan segar cenderung menurun dengan peningkatan fraksi volume butiran EPS dalam campuran.
- Kekuatan tekan beton EPS menurun seiring dengan peningkatan kandungan EPS, dengan penurunan yang lebih nyata pada kandungan EPS yang lebih tinggi. Penambahan kandungan EPS mulai dari 0% hingga 30% pada beton mengurangi kekuatan tekan beton tipe-M selama 28 hari sekitar 54%. Lebih jauh lagi, kekuatannya menurun hingga 82% ketika kandungan EPS meningkat dari 40% menjadi 70%. Beton EPS menunjukkan perilaku tegangan-regangan yang unik, berubah dari getas menjadi daktail dengan deformasi yang lebih signifikan sebelum terjadi kegagalan.
- Seiring dengan meningkatnya fraksi volume butiran EPS, maka daya alir beton EPS akan menurun. Namun, masih memungkinkan untuk mencetaknya dengan menambah jumlah superplasticizer dalam campuran kering hingga 1,5%.
- Hasil penelitian menunjukkan bahwa beton EPS berpotensi menjadi material yang cocok untuk aplikasi pencetakan 3D dalam konstruksi, dengan keunggulan seperti kepadatan yang lebih rendah dan keuletan yang lebih baik. Namun, pertimbangan cermat harus diberikan pada kekuatan tekan dan kepadatan yang dibutuhkan saat memilih campuran beton EPS.
Studi ini meneliti karakteristik beton EPS dan menemukan bahwa kekuatan, kepadatan, dan insulasi yang optimal harus dipilih berdasarkan tujuan penggunaan. Setelah campuran yang diinginkan ditentukan, campuran tersebut dapat diproduksi dan dicetak. Fleksibilitas beton EPS menghadirkan banyak peluang untuk meningkatkan teknologi pencetakan beton 3D dan memperluas aplikasinya.